Open Hours:8:30am-20:30pm
Whatsapp:+86 198-5901-3937
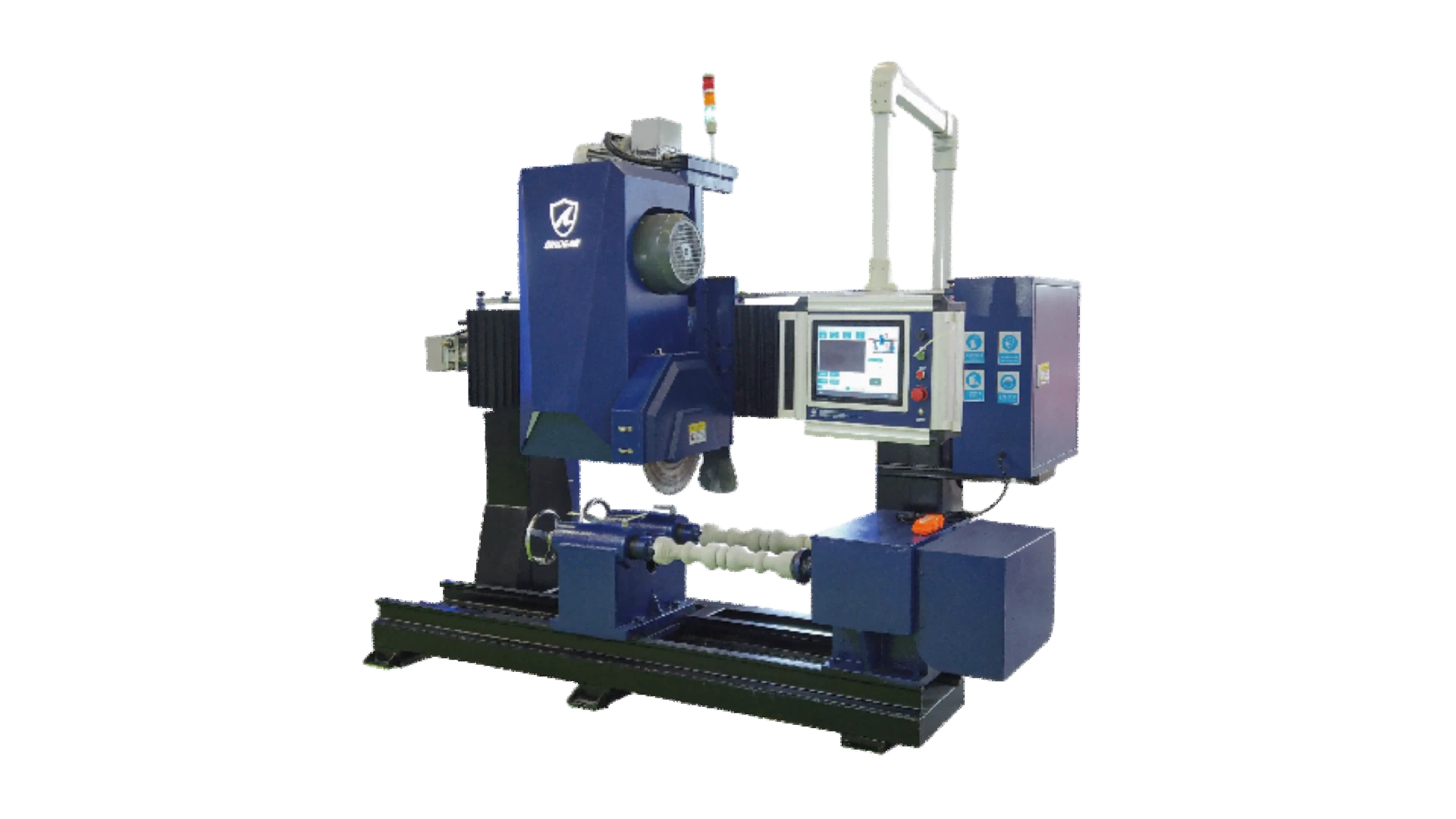




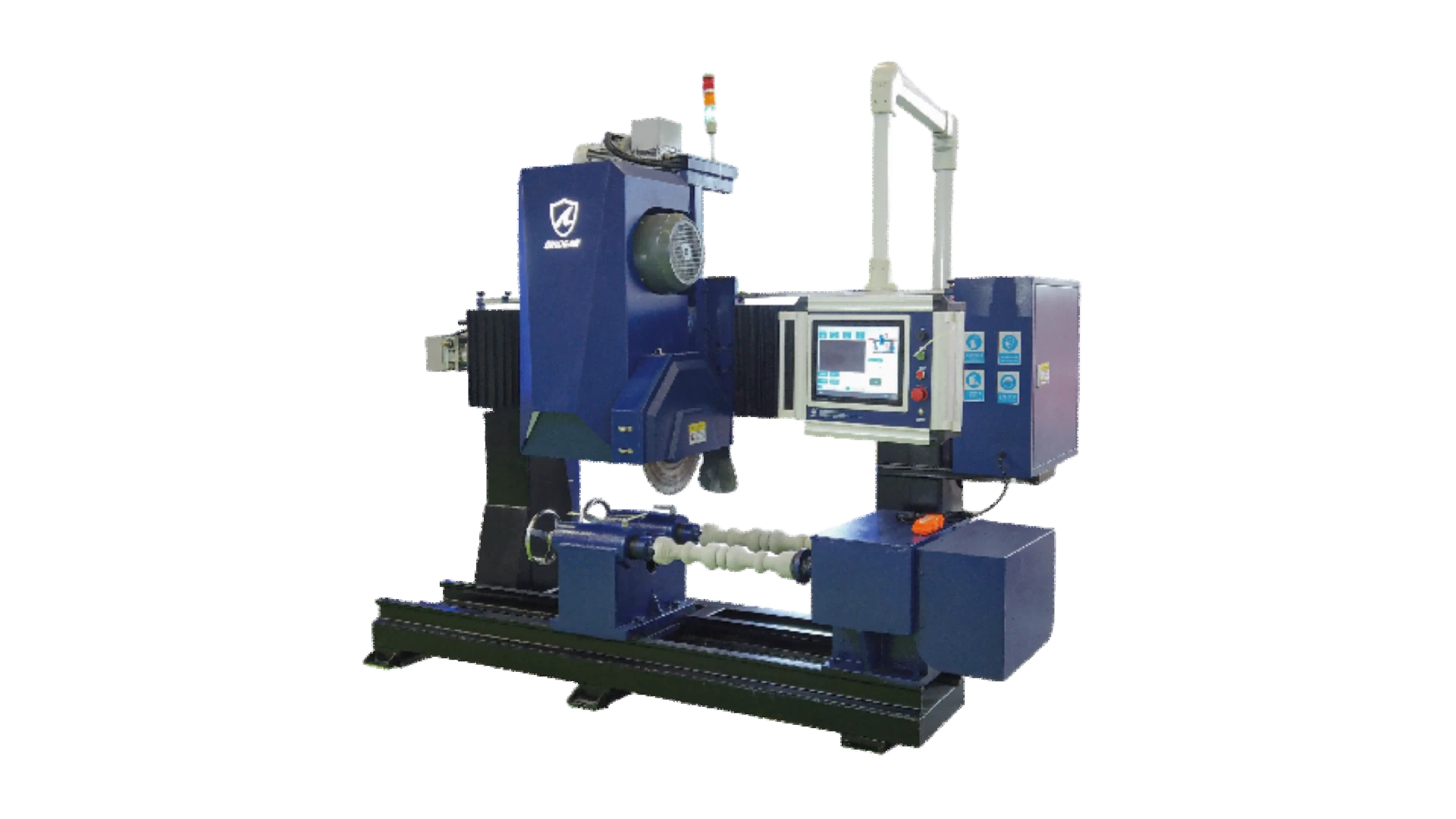




CNC Stone Lathe Machine for Balustrades and Vases
CNC Stone Lathe Machine for Balustrades and Vases
LGFX-600
LGFX-600
DINOSAW CNC stone lathe for stone turning. Ideal for granite balustrades, columns, and vases. CE-certified with automatic tool compensation. Get it today.
DINOSAW CNC stone lathe for stone turning. Ideal for granite balustrades, columns, and vases. CE-certified with automatic tool compensation. Get it today.
DINOSAW CNC stone lathe for stone turning. Ideal for granite balustrades, columns, and vases. CE-certified with automatic tool compensation. Get it today.


Share
Machine Details
Addressing Key Challenges in Stone Lathe Operations
Key Pain Points of Stone Cutting
Insufficient Profiling Accuracy
Traditional equipment struggles with ±1mm errors in ancient Egyptian-style carved balustrades, leading to 20%+ scrap rates in premium stone.

Inefficient Material Switching
Manual parameter adjustments between granite and marble cause more daily downtime.
Over-Reliance on Skilled Labor
Complex curved surface programming requires hours per project and specialized technicians.
Production Bottlenecks
Multi-step processing for ancient stone urns extends lead times by 50%.

DINOSAW's Core Value Proposition
Smart Multi-Material Compatibility
Adaptive spindle automatically adjusts parameters for black granite, marble, and engineered stone, boosting efficiency.
Zero-Programming Production
Direct CAD import (.dwg/.step) reduces programming time for stone railing carvings.

Single-Pass Forming Technology
Integrated cutting + polishing on a lathe without secondary polishing.
Technology & Competitive Advantages
Technical Specs

Operational Efficiency Gains
Tool Life Extension: Diamond blade lifespan increased via wear prediction
Energy Savings: Lower kWh consumption for stone turning lathe
Labor Reduction: 1 operator manages 3+ machines simultaneously

Select the Best Stone Lathe manufacturer:DINOSAW
Precision Revolution: ±0.5mm Accuracy Eliminates 20% Scrap Rates
DINOSAW's intelligent CNC control system achieves ±0.5mm accuracy for intricate carvings like ancient Egyptian-style balustrades, slashing scrap rates from 20%+ to <3%. Real-time wear compensation ensures flawless curved surfaces for vase capitals and columns.
Smart Material Switching: Granite-to-Marble Changeovers in 10 Minutes
Our adaptive spindle technology seamlessly handles granite, marble, and engineered stone. With 150+ preset material profiles auto-adjusting cutting speed, torque and cooling parameters, daily downtime drops by 80%.

Zero-Programming Production: CAD-to-Finished Product
Directly import .dwg/.step files – AI algorithms auto-generate toolpaths, reducing programming time for Roman column cutting from 8 hours to 5 minutes. G-code optimization eliminates redundant tool movements.
Single-Pass Forming: Cut + Polish in One Operation
Integrated diamond cutters with optional polishing setting achieve smooth finishes on heritage balustrades, eliminating secondary polishing and halving production cycles.
Global Competitiveness: Slash Energy & Labor Costs
Energy: Permanent magnet motor plus frequency converter reduces reduces stone turning energy by 40%.
Labor: 1 operator manages 3+ machines simultaneously (-70% labor costs)

Applications & Case Studies: From Royal Balustrades to Artistic Vases
Heritage Restoration:Temple Balustrade Replication
Challenge: 340 travertine balusters
Solution: 3D scan reverse engineering + batch processing
Result: 4-month completion with 98.7% historical pattern accuracy
Luxury Villa Columns: Neoclassical Marble Production Line
Configuration: LGFX-600 quad-spindle lathe (40 Corinthian capitals/day)
Tech Highlights:
≤0.3mm error on column fluting
±0.1mm auto-compensation

Artistic Stone Vases: Dynamic Curved Surfaces
Innovations:
Ultra-thin walls: 3mm minimum thickness stability
Asymmetric curves: B-spline interpolation achieves 0.01° angular precision
Municipal Projects: Granite Railing Standardization
Quanzhou Case Study:
Output: 1,200 linear meters/day of balustrades
Material utilization: Improved from 68% to 92%

Conclusion & CTA: Lead the Smart Stoneworking Era
Industry Validation:
Global stone machinery market grows at 4.7% CAGR (2023-2030), with smart equipment penetration exceeding 65%.
As a Global Stone Tech Brand , DINOSAW drives innovation with 3-month softwre upgrade and 12-month hardware upgrade cycles.
DINOSAW Offers:
✅ Customized stone turning lathe for sale
✅ Sample processing solutions
✅ Assorted diamond tools
✅ 12-month warranty + 4-hour global response
Take Action Now!📞 Call +86-19859013937/Whatsapp to get your stone lathe machine
Machine Details
Addressing Key Challenges in Stone Lathe Operations
Key Pain Points of Stone Cutting
Insufficient Profiling Accuracy
Traditional equipment struggles with ±1mm errors in ancient Egyptian-style carved balustrades, leading to 20%+ scrap rates in premium stone.

Inefficient Material Switching
Manual parameter adjustments between granite and marble cause more daily downtime.
Over-Reliance on Skilled Labor
Complex curved surface programming requires hours per project and specialized technicians.
Production Bottlenecks
Multi-step processing for ancient stone urns extends lead times by 50%.

DINOSAW's Core Value Proposition
Smart Multi-Material Compatibility
Adaptive spindle automatically adjusts parameters for black granite, marble, and engineered stone, boosting efficiency.
Zero-Programming Production
Direct CAD import (.dwg/.step) reduces programming time for stone railing carvings.

Single-Pass Forming Technology
Integrated cutting + polishing on a lathe without secondary polishing.
Technology & Competitive Advantages
Technical Specs

Operational Efficiency Gains
Tool Life Extension: Diamond blade lifespan increased via wear prediction
Energy Savings: Lower kWh consumption for stone turning lathe
Labor Reduction: 1 operator manages 3+ machines simultaneously

Select the Best Stone Lathe manufacturer:DINOSAW
Precision Revolution: ±0.5mm Accuracy Eliminates 20% Scrap Rates
DINOSAW's intelligent CNC control system achieves ±0.5mm accuracy for intricate carvings like ancient Egyptian-style balustrades, slashing scrap rates from 20%+ to <3%. Real-time wear compensation ensures flawless curved surfaces for vase capitals and columns.
Smart Material Switching: Granite-to-Marble Changeovers in 10 Minutes
Our adaptive spindle technology seamlessly handles granite, marble, and engineered stone. With 150+ preset material profiles auto-adjusting cutting speed, torque and cooling parameters, daily downtime drops by 80%.

Zero-Programming Production: CAD-to-Finished Product
Directly import .dwg/.step files – AI algorithms auto-generate toolpaths, reducing programming time for Roman column cutting from 8 hours to 5 minutes. G-code optimization eliminates redundant tool movements.
Single-Pass Forming: Cut + Polish in One Operation
Integrated diamond cutters with optional polishing setting achieve smooth finishes on heritage balustrades, eliminating secondary polishing and halving production cycles.
Global Competitiveness: Slash Energy & Labor Costs
Energy: Permanent magnet motor plus frequency converter reduces reduces stone turning energy by 40%.
Labor: 1 operator manages 3+ machines simultaneously (-70% labor costs)

Applications & Case Studies: From Royal Balustrades to Artistic Vases
Heritage Restoration:Temple Balustrade Replication
Challenge: 340 travertine balusters
Solution: 3D scan reverse engineering + batch processing
Result: 4-month completion with 98.7% historical pattern accuracy
Luxury Villa Columns: Neoclassical Marble Production Line
Configuration: LGFX-600 quad-spindle lathe (40 Corinthian capitals/day)
Tech Highlights:
≤0.3mm error on column fluting
±0.1mm auto-compensation

Artistic Stone Vases: Dynamic Curved Surfaces
Innovations:
Ultra-thin walls: 3mm minimum thickness stability
Asymmetric curves: B-spline interpolation achieves 0.01° angular precision
Municipal Projects: Granite Railing Standardization
Quanzhou Case Study:
Output: 1,200 linear meters/day of balustrades
Material utilization: Improved from 68% to 92%

Conclusion & CTA: Lead the Smart Stoneworking Era
Industry Validation:
Global stone machinery market grows at 4.7% CAGR (2023-2030), with smart equipment penetration exceeding 65%.
As a Global Stone Tech Brand , DINOSAW drives innovation with 3-month softwre upgrade and 12-month hardware upgrade cycles.
DINOSAW Offers:
✅ Customized stone turning lathe for sale
✅ Sample processing solutions
✅ Assorted diamond tools
✅ 12-month warranty + 4-hour global response
Take Action Now!📞 Call +86-19859013937/Whatsapp to get your stone lathe machine
Other Machines or Tools
Other Machines or Tools
Are you looking for more new information machines or tools?
RELATED INDUSTRY MACHINES TO BUILD YOUR PROJECTS
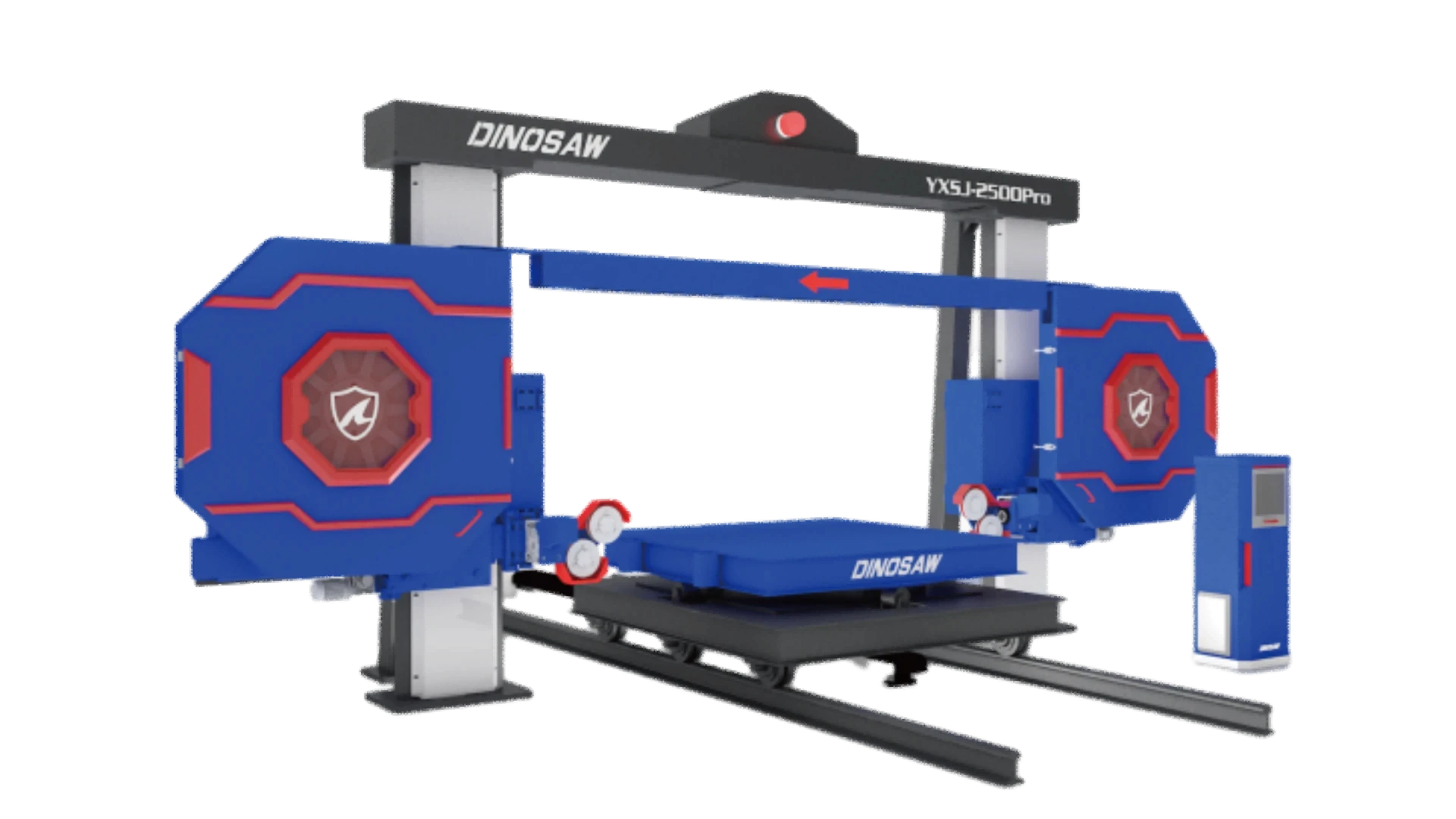
Diamond Wire Saw Cutting Machine | Industry-Leading CNC Manufacturer
Jan 11, 2025
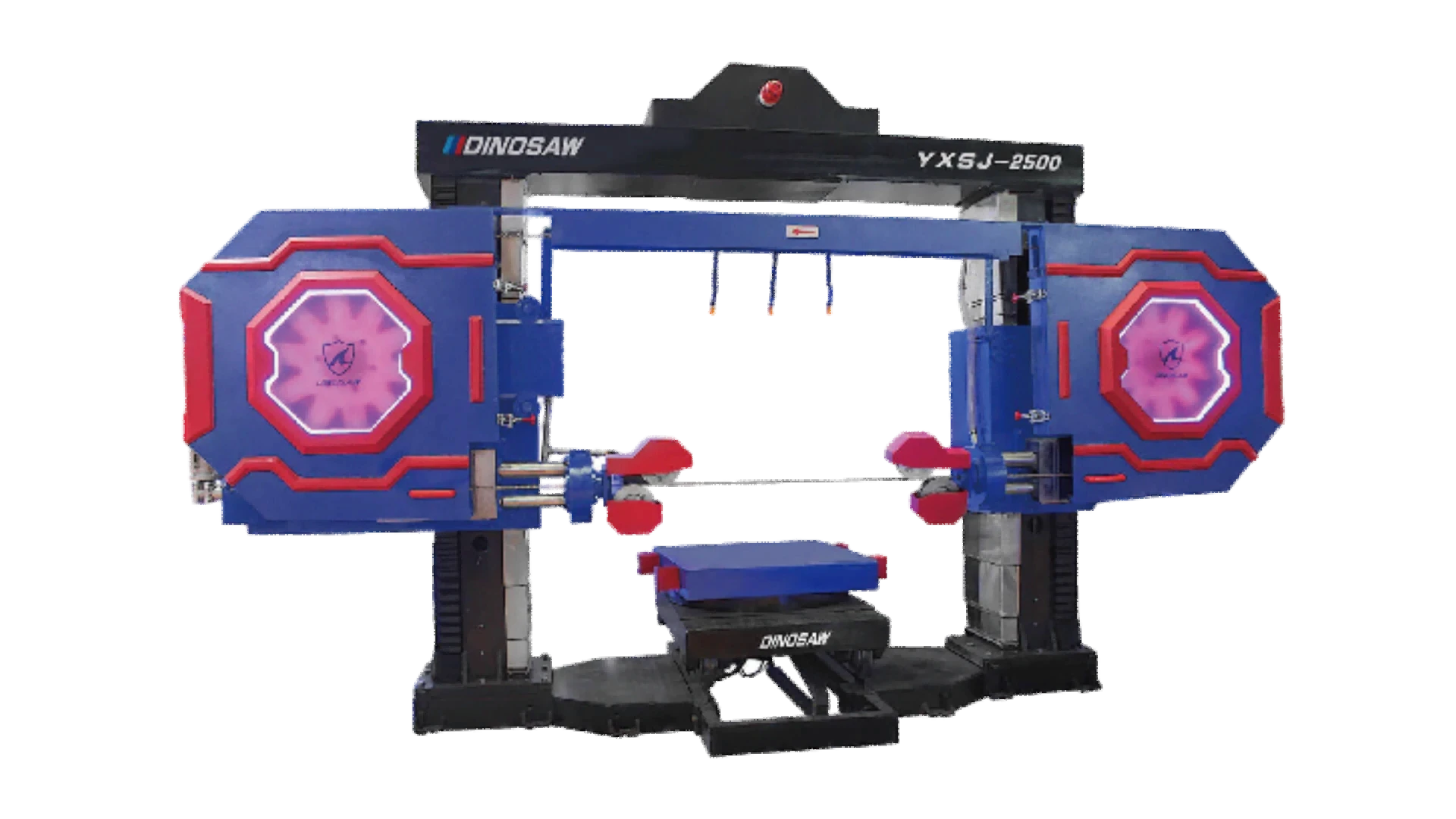
CNC Diamond Wire Saw Machine | #1 Hard Materials Cutting & Stone Profiling Expert
Jan 15, 2025
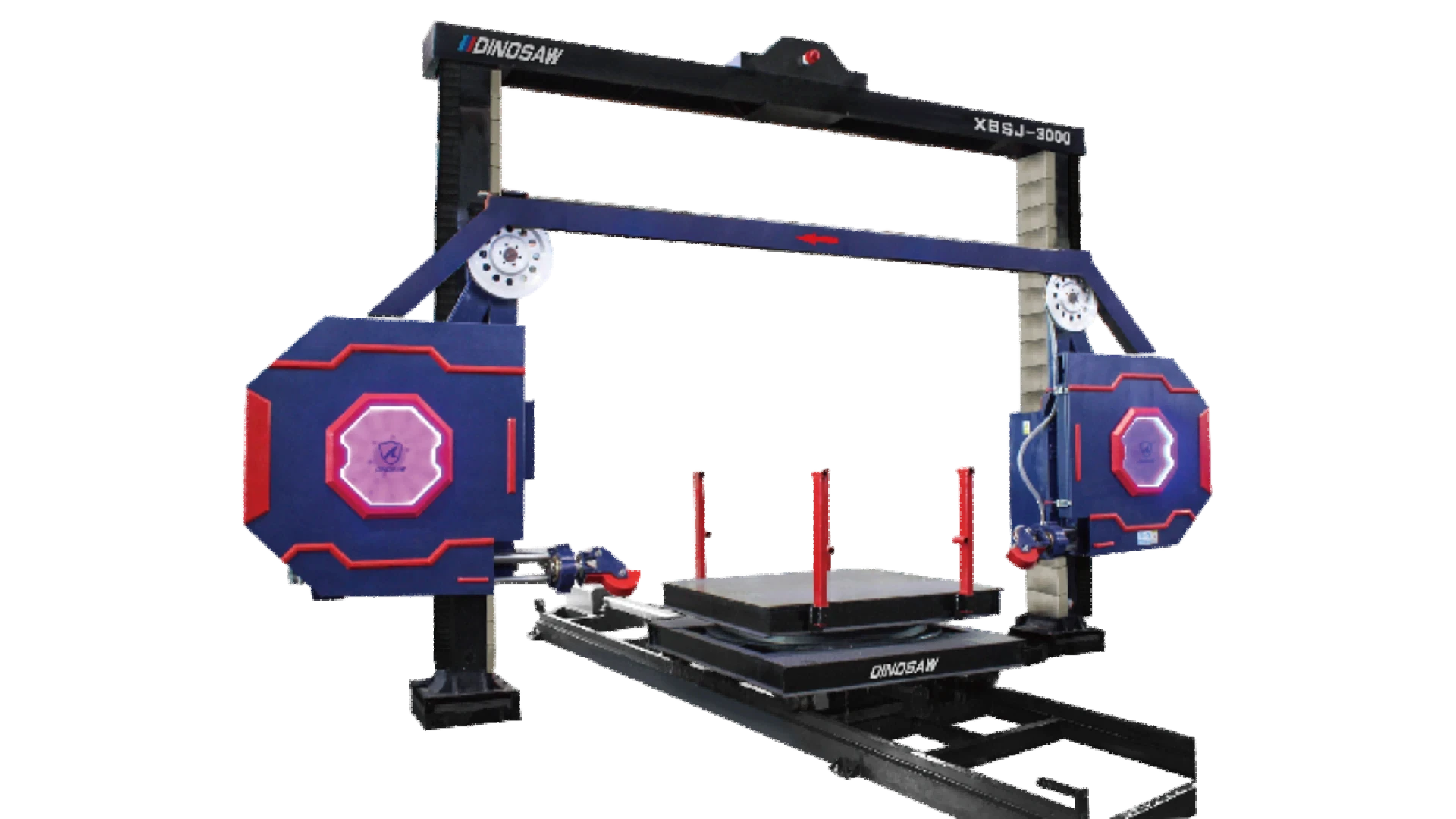
Diamond Wire Saw Granite Block Cutting Machine for sale
Dec 4, 2024
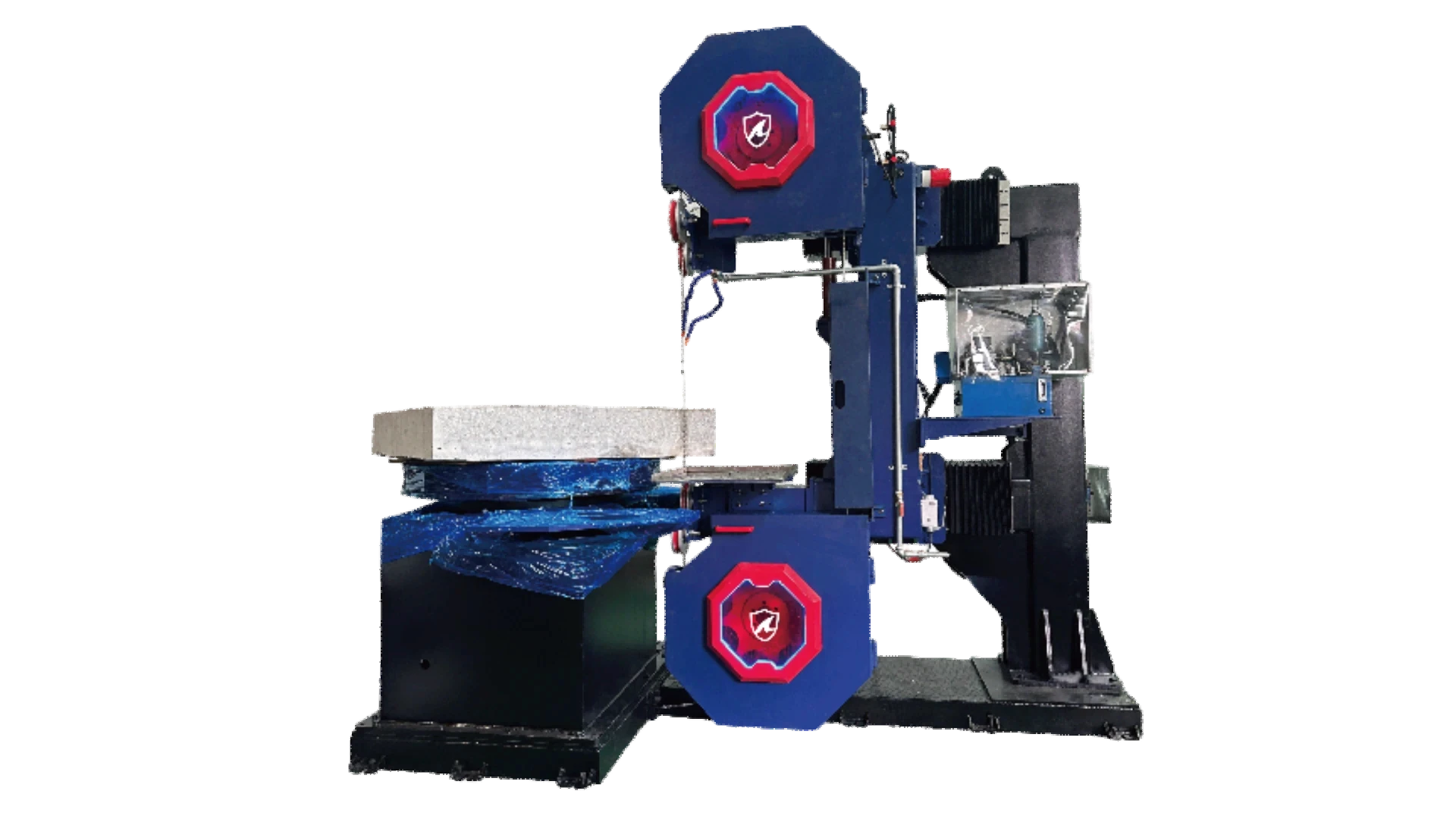
CNC Vertical Wire Saw Machine for High-Precision Cutting
Dec 8, 2024
RELATED INDUSTRY MACHINES TO BUILD YOUR PROJECTS
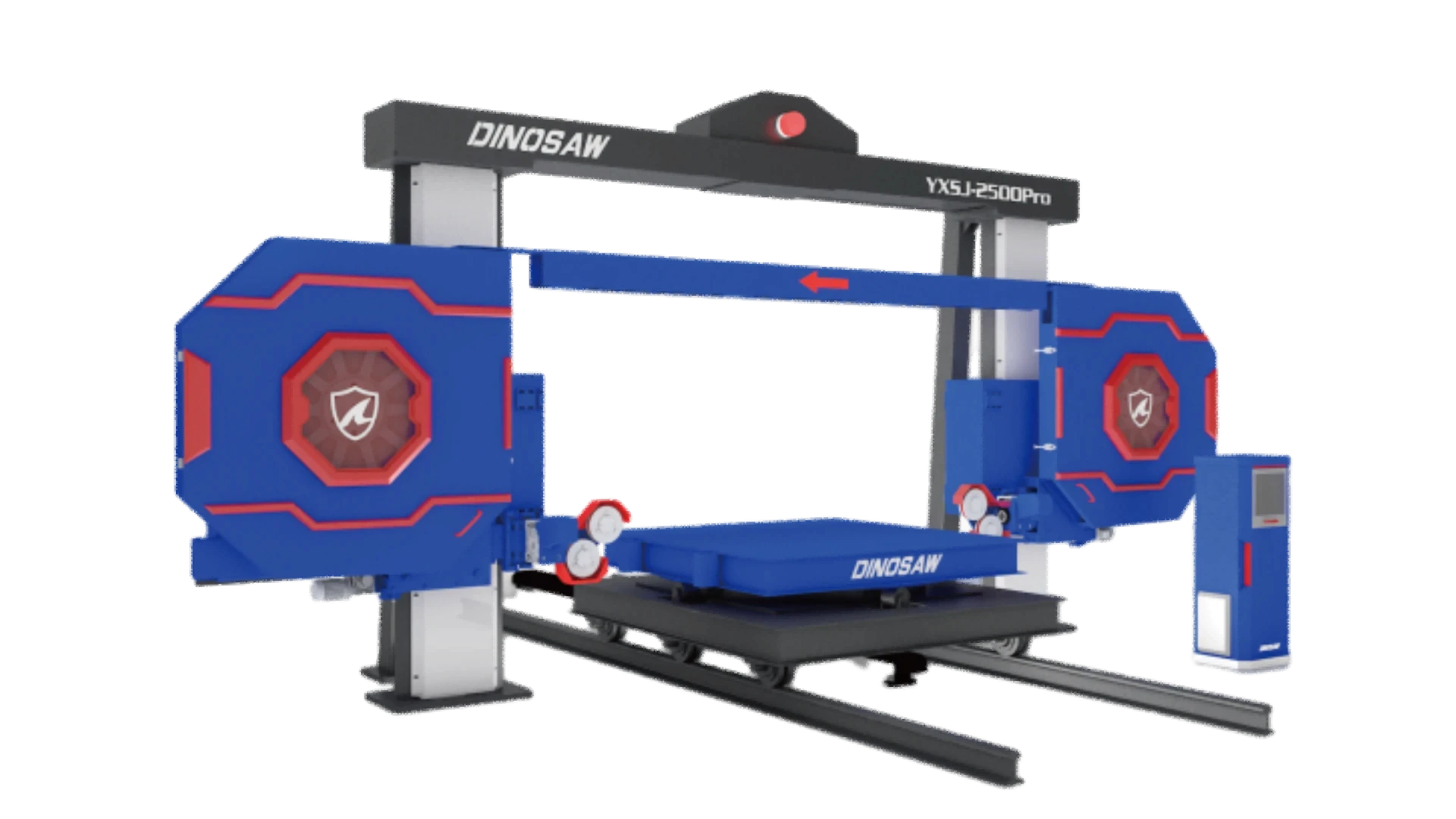
Diamond Wire Saw Cutting Machine | Industry-Leading CNC Manufacturer
Jan 11, 2025
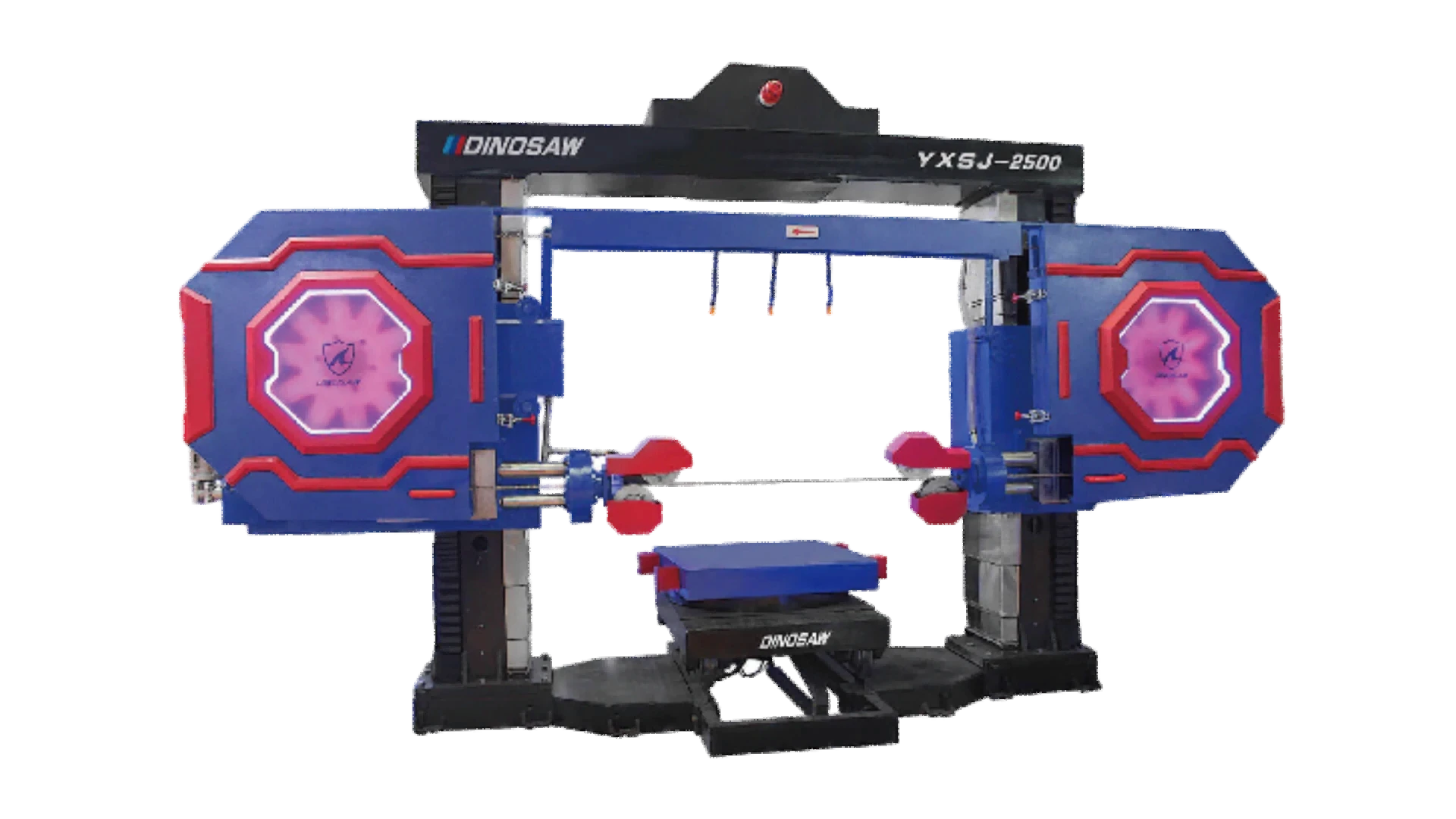
CNC Diamond Wire Saw Machine | #1 Hard Materials Cutting & Stone Profiling Expert
Jan 15, 2025
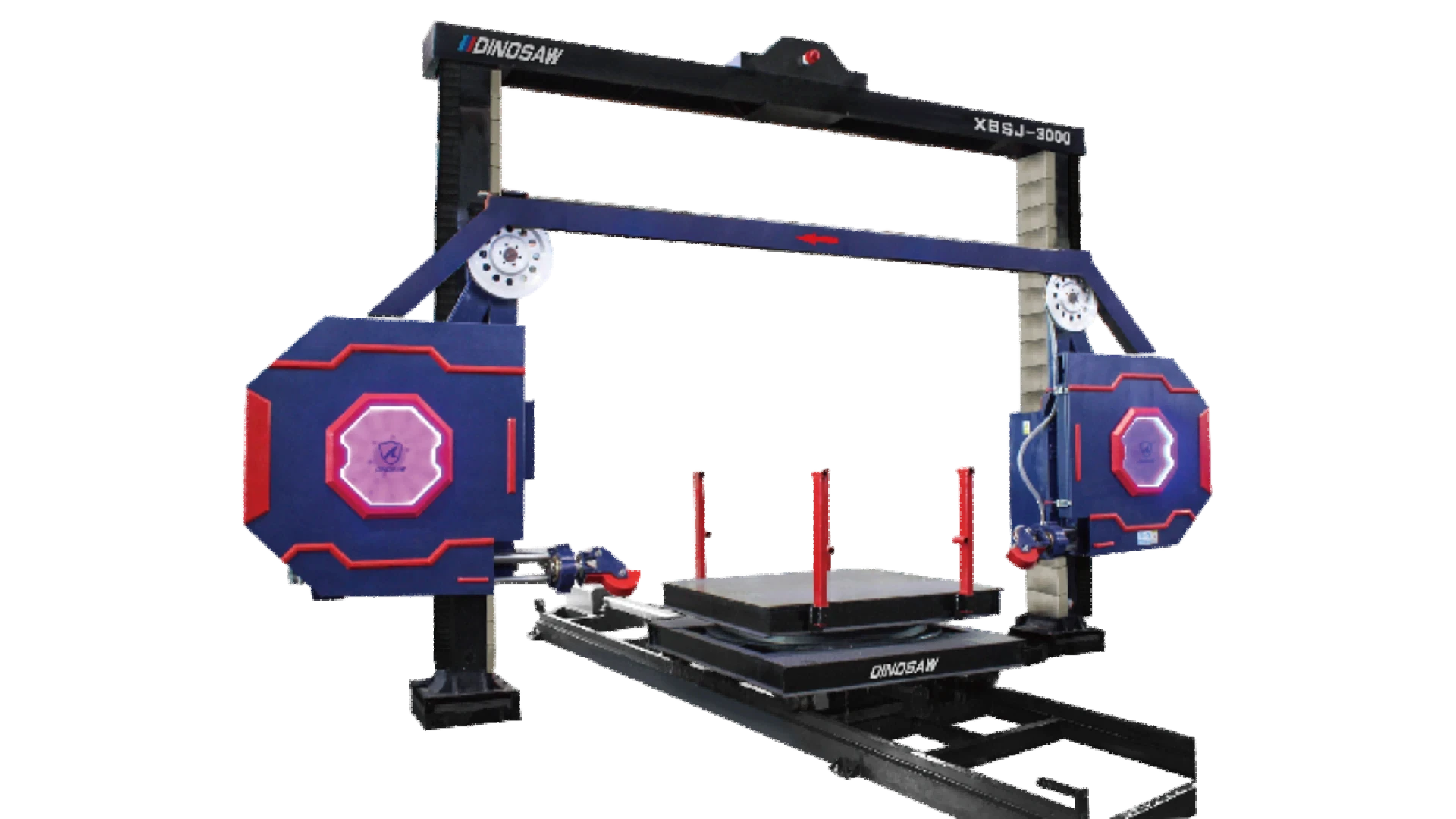
Diamond Wire Saw Granite Block Cutting Machine for sale
Dec 4, 2024
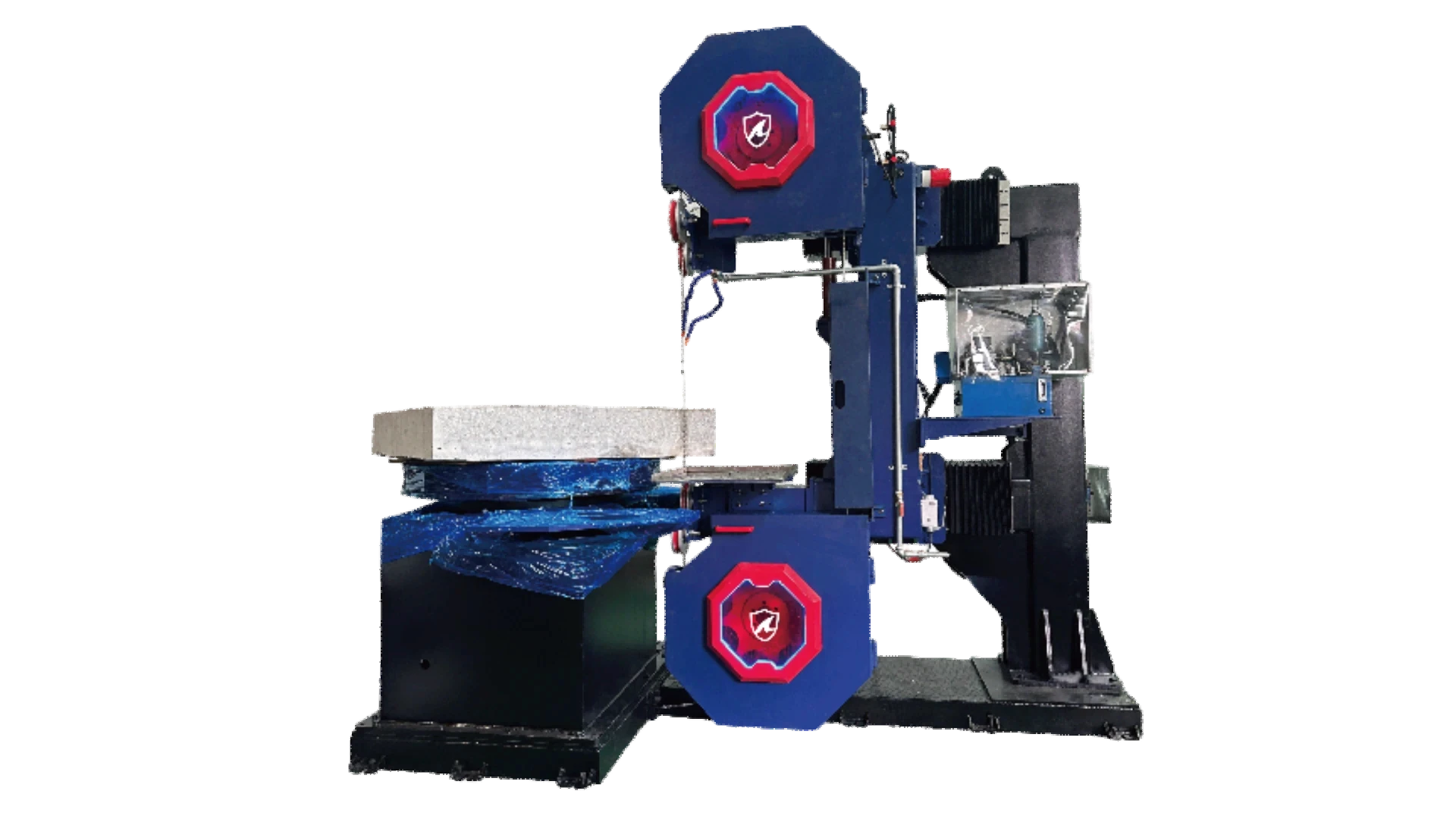
CNC Vertical Wire Saw Machine for High-Precision Cutting
Dec 8, 2024
RELATED INDUSTRY MACHINES TO BUILD YOUR PROJECTS
CONTINUOUSLY IMPROVE PRODUCTIVITY FOR USER
Customer first | Teamwork | Embrace change | Integrity | Passion | Commitment
CONTINUOUSLY IMPROVE PRODUCTIVITY FOR USER
Customer first | Teamwork | Embrace change | Integrity | Passion | Commitment
CONTINUOUSLY IMPROVE PRODUCTIVITY FOR USER
Customer first | Teamwork | Embrace change | Integrity | Passion | Commitment
CONTINUOUSLY IMPROVE PRODUCTIVITY FOR USER
Customer first | Teamwork | Embrace change | Integrity | Passion | Commitment